Applications of Thermal Oil Heating Systems in the Pharmaceutical Industry
The heating temperature requirements in the pharmaceutical industry are very diverse, as different pharmaceutical processes and product preparation steps have different temperature requirements. The following are some of the heating temperature ranges involved in typical pharmaceutical processes:
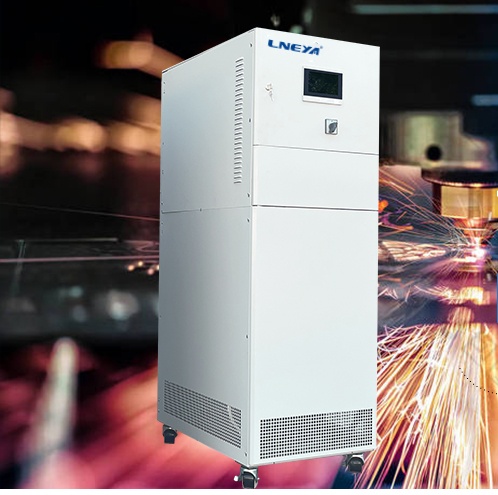
Reactor Heating: In chemical synthesis reactions, the heating temperature may range from room temperature to several hundred degrees, depending on the type of chemical reaction being performed. In the drug synthesis process, the thermal oil heating system provides a stable and uniform heat source for the reactor to ensure that the chemical reaction is carried out at a precisely controlled temperature, which is critical to maintaining product quality and improving reaction efficiency. For example, some esterification reactions may require temperatures between 80°C and 120°C, while some reactions that require higher temperatures may approach 200°C. Reactors are usually equipped with temperature control systems that can accurately control the reaction temperature.
Drying and Drying: When drying APIs, intermediates or finished products, the temperature range may be between 50°C and 200°C, depending on the nature of the material and the drying requirements. In the pharmaceutical process, APIs, intermediates or finished products often need to go through a drying or drying step to remove moisture. Thermal oil circulation systems can efficiently provide heat energy to equipment such as dryers and ovens to ensure that the drying process is both fast and uniform, while avoiding the destruction of heat-sensitive components caused by direct heating. For example, vacuum drying may be carried out at a lower temperature, while spray drying may involve higher temperatures.
Melting and Crystallization: When preparing solid drug forms, such as tablets and capsule fillings, thermal oil heating systems are used to melt raw materials for subsequent molding and processing. Similarly, it is also used in crystallization processes under temperature control to optimize crystal morphology and purity. In the production of solid dosage forms, the hot melt granulation process may require the material to be heated above its melting point, usually in the range of 80°C to 200°C, depending on the melting point of the material used. In crystallization operations, temperature control is very critical and may require fine adjustment from room temperature to low temperatures (such as -5°C to room temperature) to promote the formation of specific crystal forms.
Sterilization and Disinfection: In certain sterilization or disinfection processes, thermal oil circulation systems can provide the necessary heat for sterilization equipment to ensure sterile conditions and meet GMP (Good Manufacturing Practice) requirements.
Coating: During the tablet coating process, the hot air temperature may be controlled between 30°C and 80°C to ensure the correct melting and uniform coating of the coating material.
Hot Melt Extrusion: When producing solid preparations such as sustained-release tablets, enteric coatings, etc., hot melt extrusion technology requires precise temperature control. The thermal oil heating system can provide a stable heat source for the extruder to ensure the uniformity of the molten material, affecting the physical properties and drug release characteristics of the final product.
Heat Treatment and Heat Exchange: In pharmaceutical equipment such as heat exchangers and heat exchange systems, thermal oil is used as a medium to efficiently transfer heat energy for heating or cooling to ensure temperature control of materials during processing.
The thermal oil heating system has become an indispensable part of the pharmaceutical industry with its stable, safe and efficient characteristics. It not only ensures precise control of the production process, but also improves production efficiency and product quality, while reducing production costs and environmental impact.
Related recommendations
-
Which equipment does a chemical plant use a heating circulator to heat?
283In chemical plants, heating circulators are widely used to heat a variety of key equipment and devices to ensure that chemical reactions and processes are carried out under suitable temperature conditions. The following are some of the mai...
View details -
The role of recirculating heaters in chemical and biological reaction instruments
285Temperature Control: The recirculating heater provides a precise and stable temperature control environment, which is a crucial factor in chemical and biological reactions. Different chemical reactions and biological processes have spec...
View details -
UC series
2648WhatsApp: 86 13912479193 WeChat 86 15152266993 Fully enclosed system, heat transfer oil will not be oxidized or browning ...
View details -
Why do semiconductor manufacturing companies need heating circulator equipment?
285Temperature Control Accuracy: The semiconductor manufacturing process has extremely strict requirements for temperature control. The heating circulator can provide precise temperature control, ensuring that the temperature remains withi...
View details