What tests are used by cooling water chillers for new energy enterprises?
In the process of product development, production and quality control, new energy enterprises will use cooling water chillers to perform a variety of tests. Cooling water chillers play an important role in these tests to ensure the performance, reliability and safety of products.
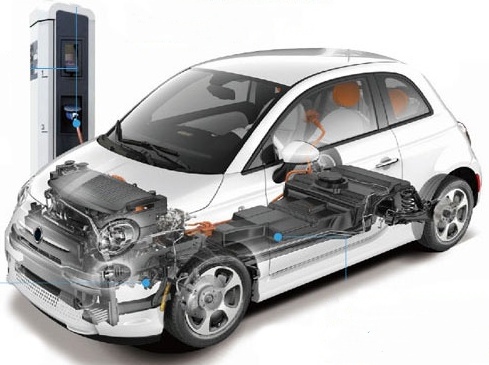
The following are some typical tests that new energy enterprises use cooling water chillers for:
Battery pack testing:
- Thermal cycle test: simulate the cycle changes of battery packs under different temperature conditions to evaluate the thermal cycle performance of battery packs.
- Thermal shock test: simulate the situation where the battery pack undergoes a sharp change in temperature in a short period of time to evaluate the thermal stability of the battery pack.
- Temperature dependence test: evaluate the performance of the battery pack under different temperature conditions, such as charging and discharging capacity, energy density, etc.
- Thermal management system test: evaluate the performance of the thermal management system of the battery pack under different temperature conditions to ensure that the battery pack can effectively dissipate heat.
Motor testing:
- Temperature dependence test: evaluate the performance of the motor under different temperature conditions, such as speed, torque, etc.
- Thermal cycle test: simulate the cycle changes of the motor under different temperature conditions to evaluate the thermal cycle performance of the motor.
- Thermal management system test: evaluate the performance of the thermal management system of the motor under different temperature conditions to ensure that the motor can effectively dissipate heat.
Power electronic equipment test:
- Inverter and frequency converter test: evaluate the performance of power electronic equipment under different temperature conditions, such as conversion efficiency, reliability, etc.
- Thermal cycle test: simulate the cycle changes of power electronic equipment under different temperature conditions to evaluate the thermal cycle performance of the equipment.
- Thermal management system test: evaluate the performance of the thermal management system of power electronic equipment under different temperature conditions to ensure that the equipment can effectively dissipate heat.
Energy storage system test:
- Battery energy storage system test: evaluate the performance of the battery energy storage system under different temperature conditions, such as charging and discharging capacity, energy density, etc.
- Thermal management system test: evaluate the performance of the thermal management system of the energy storage system under different temperature conditions to ensure that the energy storage system can effectively dissipate heat.
Fuel cell test:
- Thermal cycle test: simulate the cycle changes of fuel cells under different temperature conditions to evaluate the thermal cycle performance of fuel cells.
- Thermal management system test: evaluate the performance of the thermal management system of fuel cells under different temperature conditions to ensure that the fuel cells can effectively dissipate heat.
Electric vehicle component testing:
- Electric vehicle motor controller testing: Evaluate the performance of the motor controller under different temperature conditions.
- Battery management system (BMS) testing: Evaluate the performance of the battery management system under different temperature conditions.
- Thermal management system testing: Evaluate the performance of the electric vehicle thermal management system under different temperature conditions.
Environmental simulation testing:
- Temperature cycle testing: Simulate the cyclic changes of the product under different temperature conditions to evaluate the thermal cycle performance of the product.
- Thermal shock testing: Simulate the situation where the product experiences a sharp change in temperature in a short period of time to evaluate the thermal stability of the product.
- High and low temperature testing: Simulate the performance of the product under extreme temperature conditions to evaluate the performance of the product.
Summary Cooling water chillers play a key role in the testing of new energy companies, ensuring the performance, reliability and safety of the products by providing precise temperature control. These tests help optimize product design, improve product quality, and ensure that the products can perform well under actual use conditions.
LNEYA’s KRY series water chillers can remotely monitor test data to ensure that the system’s operating data can be obtained remotely. Data records include temperature, pressure, flow, etc. It comes with an emergency stop button, which can quickly and safely stop operation in an emergency. It can also be used for cooling inverters in photovoltaic power stations, etc.
Refrigeratore d'acqua di raffreddamento-40℃~100℃
KRY -40℃~+100℃ (1to6)
Product data downloadtemperature control, flow controlParameters DetailedProductDescriptionrecommend products The components are cooled and heated internally through ethylene glycol aqueous solution for testing -40 ° …
KRY -40℃~+100℃ (1to1)
Temperature control in the testing process of new energy vehicle componentsParameters DetailedEquipment appearanceGeneral equipmentMultichannel equipmentMulti channel independent temperature controlVariable frequency regulationClient AClient BAppl…
KRY -40℃~+100℃ (1to2)
Product data downloadParameters DetailedProductDescriptionYou may also be interested in these products Temperature range is -40℃~+100℃, which can be extended to +135℃ according to the actual situation, and the temperature contro…
KRY -40℃~+100℃ (1to3)
Product data downloadKRY -40℃~100℃ 1&3S (3 sets of auxiliary temperature control, Pressure/Flow controlled separately)ProductDescriptionYou may also be interested in these products Dimension(A) cm Temperature r…
caricamento...
已经是到最后一篇内容了!
Refrigeratore d'acqua di raffreddamento0℃~100℃
KRY 0℃~+100℃ (1to2)
Product data downloadParameters DescriptionProductDescriptionYou may also be interested in these products Temperature range is 0℃~+100℃, which can be extended to +135℃ according to the actual situation, and the temperature c…
KRY 0℃~+100℃ (1to3)
Product data downloadKRY 0℃~100℃ 1&3S(3 sets of auxiliary temperature control, pressure/flow controlled separately)ProductDescriptionYou may also be interested in these products Test temperature of main test items …
KRY 0℃~+100℃(1&6)
Product data downloadKRY 0℃~100℃ 1&6S(6 sets of auxiliary temperature control, pressure and flow controlled separately)ProductDescriptionWorking PrincipleYou may also be interested in these products Temperatur…
KRY 0℃~+100℃ (1to1)
Product data downloadParameters DetailedProductDescriptionWorking PrincipleYou may also be interested in these products Temperature range is 0℃~+100℃, which can be extended to +135℃ according to the actual situation, and the tem…
caricamento...
已经是到最后一篇内容了!